Reducing CO₂ Emissions
The increasing severity of climate change is leading to numerous issues, including direct health hazards caused by temperature extremes, insufficient water resources, and an accelerated loss of biodiversity. For responding to Climate Change, the world leaders gathered at the COP26 summit agreed to limit global temperature rises to 1.5°C.
In accordance with the TCFD framework, Shiseido discloses information on the financial impact that long-term climate-related risks and opportunities may have on its business. Moreover, to ensure a thorough response to these risks―and to leave a better environment for future generations―we support the Paris Agreement and the Glasgow Climate Pact, and have set goals following the Science Based Targets initiative, which aims to cut CO₂ emissions in line with the 1.5°C. target ahead of 2030. Our CO₂ reduction goals were accredited by the Science Based Targets initiative in 2022.
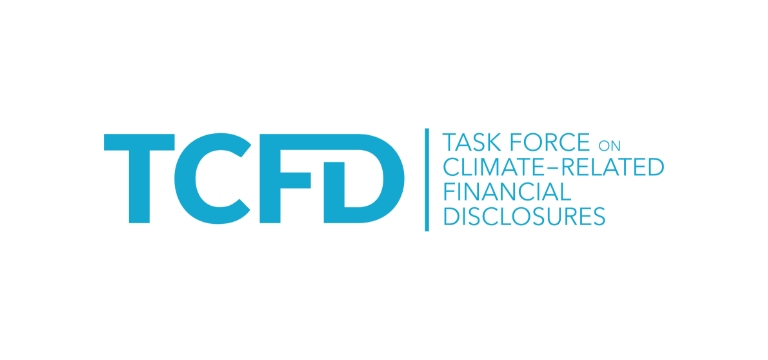
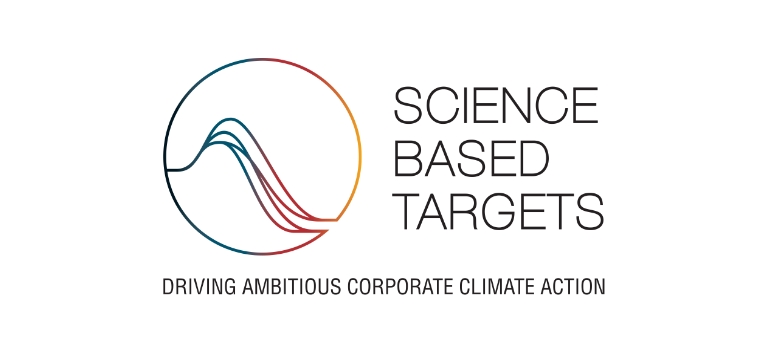
Reducing CO₂ Emissions from Energy Consumption (Scope 1 and 2)
To mitigate climate change, we are committed to reducing CO₂ emissions from the electricity and fuel used in our business activities. As part of our efforts, we use renewable energy where possible and constantly seek to improve energy efficiency in our factories, offices, and other facilities.
Increasing the Use of Renewable Energy
We are constantly working to increase the use of renewable energy at our factories and offices. By the end of 2022, all our factories (both domestic and overseas) operated on 100% carbon neutral electricity. In addition, we are promoting the use of renewable energy in our offices, such as switching 100% of the electricity at our Shiodome and Ginza headquarter offices to renewable electricity. As a result, renewable electricity now accounts for 75% of all the electricity used at Shiseido Group.
In addition to promoting the use of renewable energy, we are installing solar panels on the premises and in the buildings of our factories and research centers worldwide. In 2022, our Fukuoka Kurume factory, Osaka Ibaraki factory (both in Japan) and Taiwan factory were equipped with solar panels, and now nine of our factories are equipped with solar power generation facilities.
Shiseido is a member of the RE100 global initiative, which brings together businesses committed to using 100% renewable electricity in their activities. We will continue to accelerate our transition to renewable electricity in our operations to reduce fossil-fuel derived electricity.
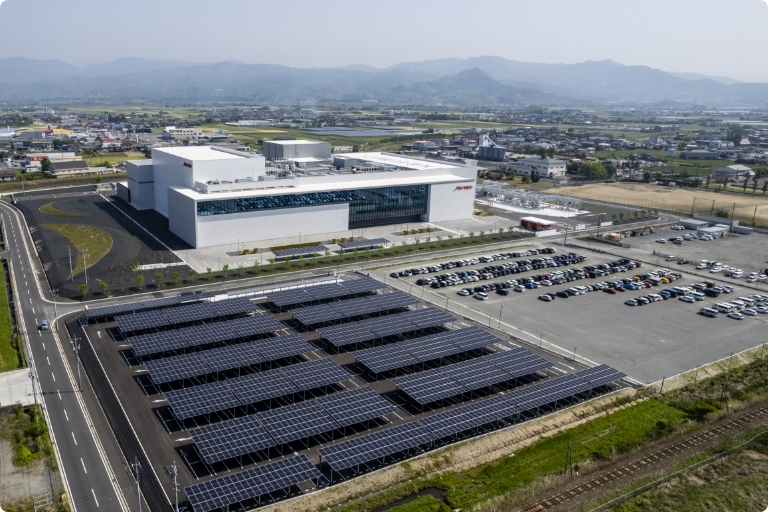
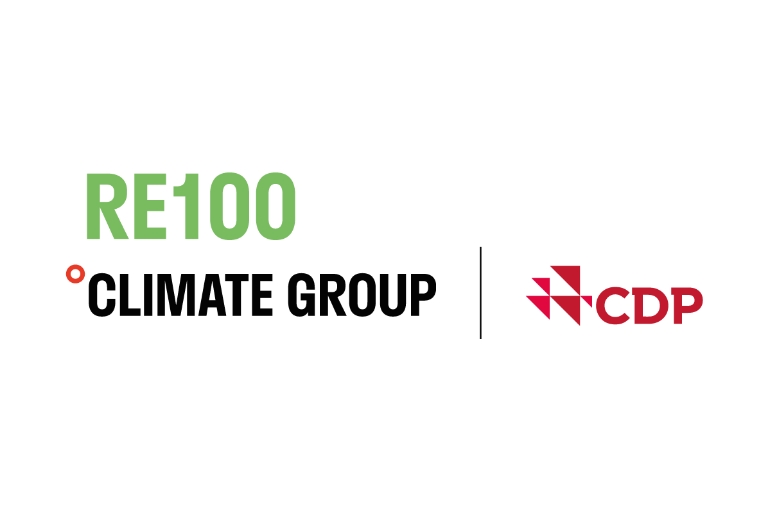
Improving Energy Efficiency
To increase energy efficiency, we are introducing several building design improvements at our factories, including improved heat insulation, more energy-efficient equipment, and new environmental measures based on the ISO 14001 environmental management system.
In addition to using LED lighting to reduce energy consumption, we installed Energy Management Systems (EMS) to visualize energy use and CO₂ emissions on equipment that uses electricity, steam, or compressed air. These systems allow us to optimize energy usage in a number of ways and, in this way, help us to reduce energy consumption.
Furthermore, at our Osaka Ibaraki factory and neighboring West Japan Distribution Center — our production and logistics hub in Japan — we installed sandwich panels in the exterior walls. Lightweight and with excellent heat insulation properties, these panels have helped reduce CO₂ emissions generated by operations at the facilities by approximately 30%.
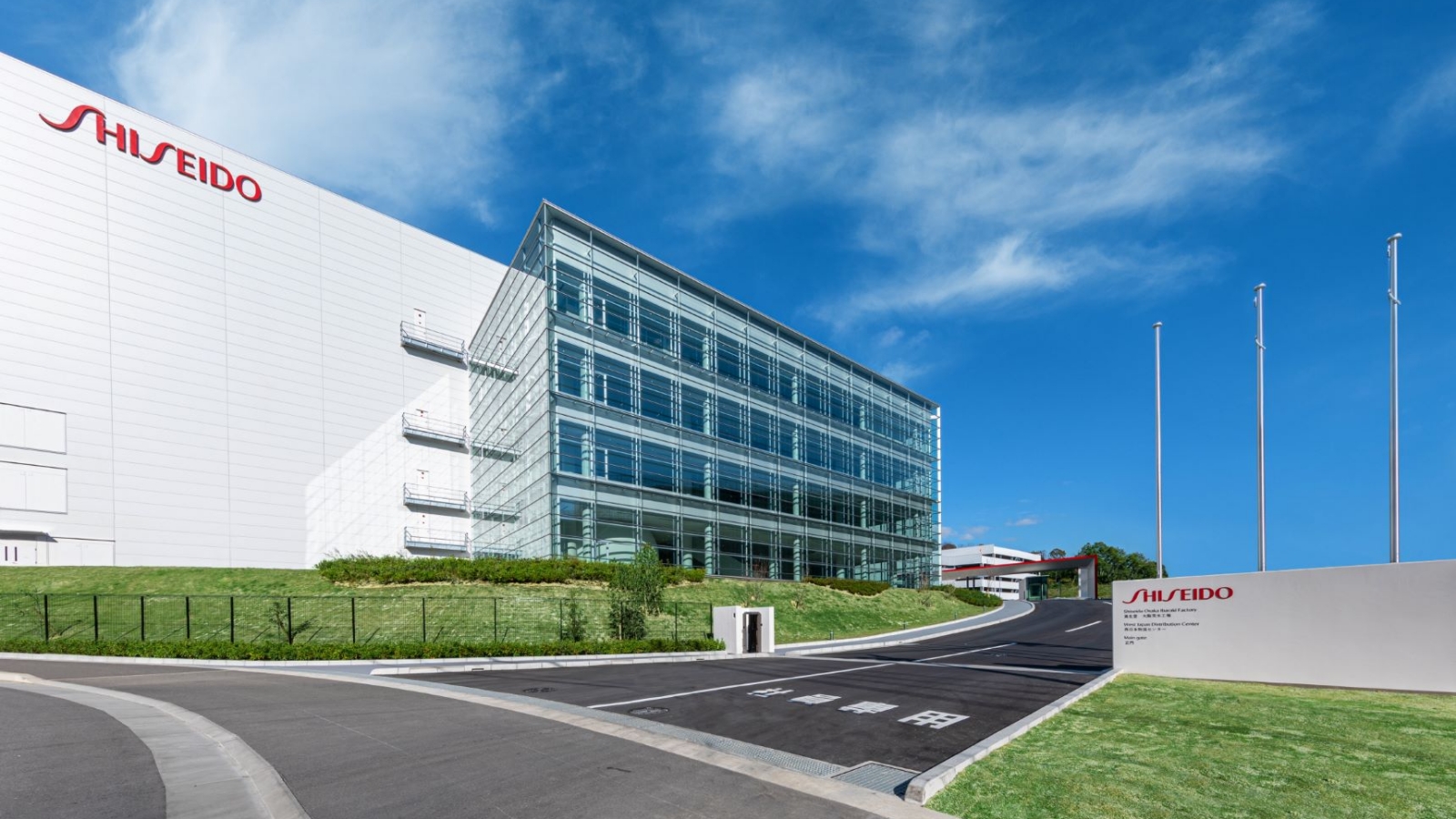
Kakegawa Factory Initiative Wins the Director General Prize for Agency of Natural Resources and Energy
Our Kakegawa factory in Japan was awarded the Director General Prize for Agency of Natural Resources and Energy (Energy Conservation Best Practices Category) at the Energy Conservation Grand Prize 2022. The Energy Conservation Grand Prize recognizes outstanding energy-saving initiatives and advanced, high-efficiency energy-saving products in Japan’s industrial, business, and transportation sectors.
We received this prize for our energy-saving activities at our Kakegawa factory. These include an initiative to achieve carbon neutrality of electricity in cosmetics manufacturing by enabling factory employees to proactively participate in energy-saving projects. As a result of our work, we reduced CO₂ emissions at our Kakegawa factory by 9.5% in 2021 compared to 2019.
The prize recognized the initiatives at the Kakegawa factory for their outstanding versatility. They can be transferred to other sectors, and so have the potential to accelerate energy-saving measures in other industries.
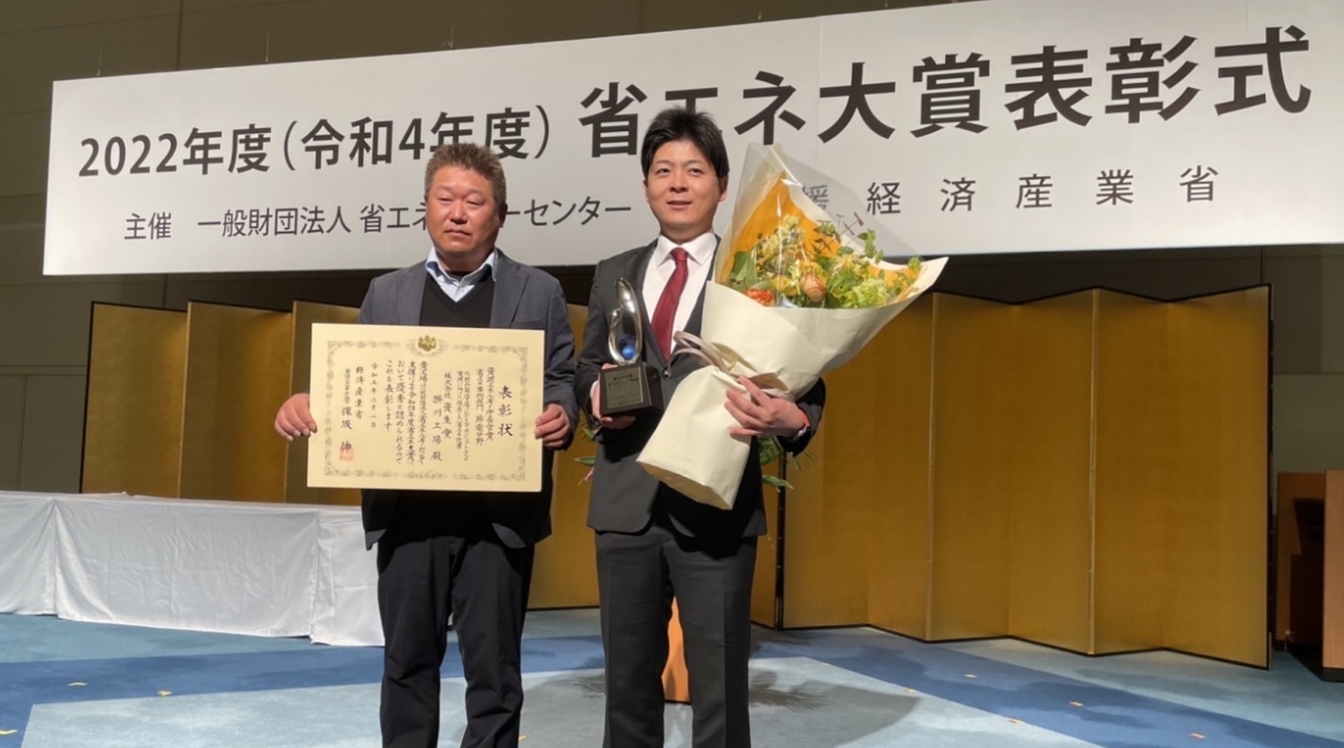
Reducing Indirect CO₂ Emissions from the Value Chain (Scope 3)
Our indirect CO₂ emissions also result from our business activities but they are not directly under our control – for example, emissions that derive from the manufacturing and shipping of raw materials or the use and disposal of our products. As part of our work to reduce the impact of our business activities on climate change, we have established science-based long-term reduction targets for our indirect CO₂ emissions, and we are working with our suppliers and other stakeholders to reduce emissions across our entire value chain.
Procurement of Raw Materials
In line with the green chemistry principles, we select raw materials that generate low CO₂ emissions, just as we strive to reduce CO₂ emissions during product development. With regard to palm oil-derived materials, which are key ingredients in our products, as well as sugarcane-derived polyethylene and paper for containers, we use raw materials that are not linked to deforestation.
In 2022, Shiseido participated in the CDP Supply Chain Program. Through the program, we expect to reduce CO₂ emissions related to raw material procurement. In 2023, we will begin to monitor our suppliers’ CO₂ emissions and engage with them to reduce emissions.
Reducing CO₂ Emissions During Transportation
Shiseido is striving to reduce waste and CO₂ emissions by repeatedly using shipping boxes when procuring materials, mainly from bottle suppliers that deliver frequently.
When shipping our own products, we conduct joint deliveries with other domestic companies to optimize transportation routes and improve loading efficiency. In addition, since in 2022, we began double stack palletization for our exports from Japan to overseas destinations, improving loading efficiency. We also optimize the use and design of packaging materials according to the shape and volume of the products shipped and actively promote the reuse of protective materials used in transportation.
In February 2023, we introduced an electric truck into our vehicle fleet in Japan on a trial basis. The electric truck is expected to reduce CO₂ emissions by 1 ton per year, and we plan to expand our fleet of electric vehicles moving forward.
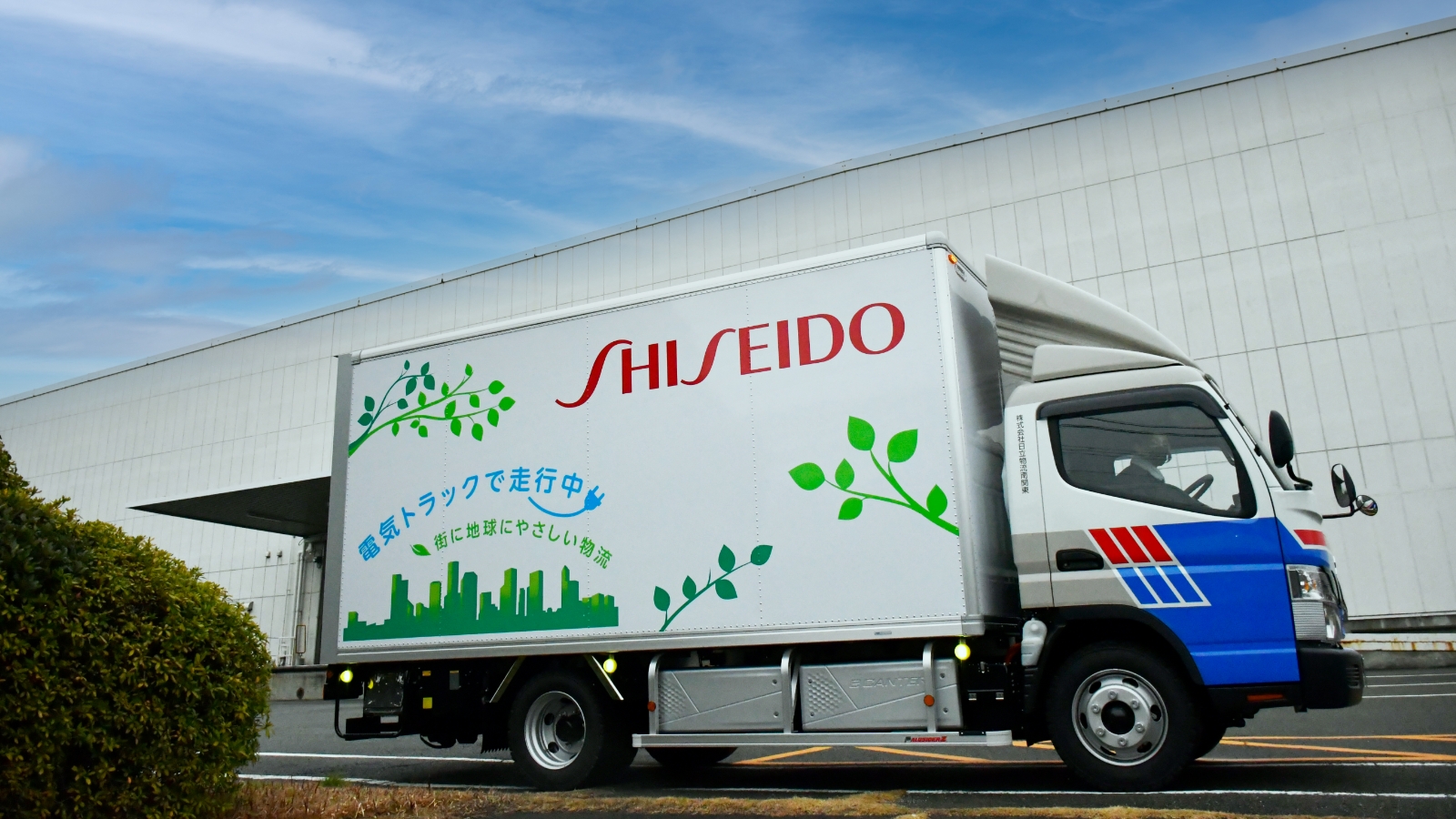
Reducing Water Consumption
Water supports every aspect of our products, including the development of water-containing products such as lotions; the growth of plants as raw materials; temperature control and equipment cleaning at factories; consumption; and waste disposal.
In view of the importance of water resource management(Water Stewardship) , we cooperate with stakeholders to promote the sustainable use of water resources by working to understand the water cycle and the environment of watersheds, reduce water consumption, increase the effectiveness of its use, and ensure thorough control of water quality. In addition, we prioritize the healthy circulation of water in water systems, value unique regional water-related cultures, and respect people’s right to safe drinking water and sanitation. At the same time, we work to educate our employees on water-saving measures, and encourage our stakeholders, including our employees, to contribute to achieving Goal 6 of the UN Sustainable Development Goals.
Water Saving Initiatives
We actively work to reduce water consumption at all our factories. As each Shiseido factory has various facilities and equipment tailored to the kind of cosmetics it produces, we design specific water reduction initiatives for each site.
Examples of our water-saving initiatives include using automatic cleaning to ensure the manufacturing equipment is cleaned more effectively, consolidating the washing locations of equipment parts, and redesigning the nozzles on our cleaning facilities. At our Val de Loire factory in France–an area where rainfall is expected to drop in future–initiatives like these successfully reduced the amount of water used per clean by 30%.
When we build new facilities, we incorporate water-saving processes in the design. This measure has a significant impact. For example, we expect our Fukuoka Kurume factory in Japan, which began operations in 2022, will use around 6,600 tons less water per year than equivalent factories, as well as expecting around 466 fewer hours on cleaning.
To ensure more effective use of water, we focus on circular systems that clean water and reuse or recycle it within the process. At our Taiwan factory, for example, we reuse 100% of the wastewater from our water purification systems in onsite facilities. At our Osaka Ibaraki factory in Japan, we introduced a circular system that utilizes re-used water to cool the manufacturing tanks. This system led to an annual reduction in water consumption of around 65,000 ㎥ in 2022. Other new water utilization initiatives include optimizing our pure water manufacturing equipment — as we have done at our Nasu factory in Japan, for example. Pure water manufacturing consumes approximately half of all water used at the factory. Through this initiative, as well as other water recycling schemes, we reduced our annual water consumption by around 72,000 ㎥, an amount that is approximately one third of the factory’s annual water usage.
At our Gien factory in France, we switched from water-based cleaning to alcohol-based cleaning for our fragrance manufacturing equipment and transportation components. The alcohol used is cleaned and reused in the process repeatedly.
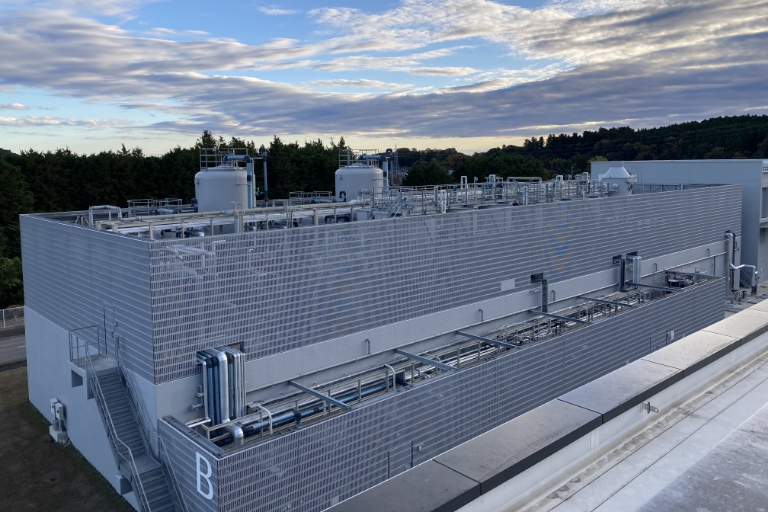
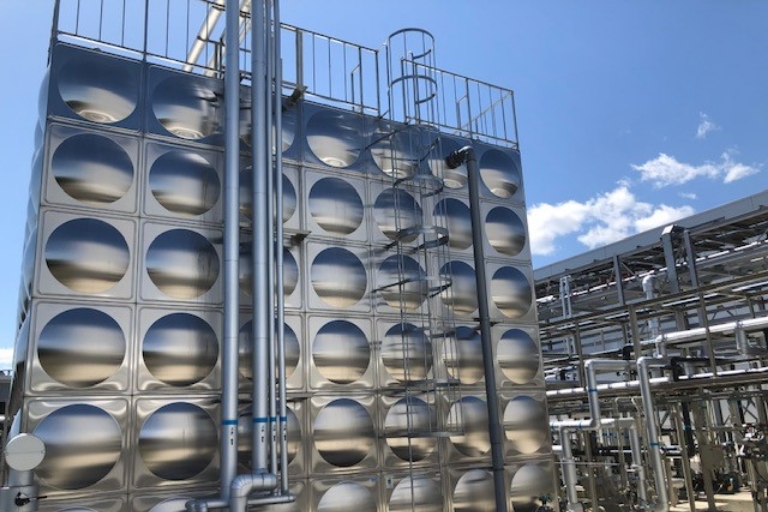
Engaging Stakeholders
To effectively use water resources, we are engaged in the management of water resources as common property of the water basin, including secondary use in cooperation with communities.
At our Nasu factory in Japan, we use high-quality groundwater for manufacturing processes and as a raw material for cosmetics. In consideration of the natural environment, the Nasu factory has established its own strict standards to control discharged water, thereby minimizing any impact on the environment and striving to coexist with nature. We regularly engage with local governments and related organizations to discuss the local water resource environment and appropriate water use at this factory.
At our Shanghai factory in China–which is located in a water-stressed area–we participate in a local environmental protection association and proactively obtain environmental information, such as environmental laws and regulations regarding factory activities. We also report monthly water consumption to the government, which promotes water conservation and is working to improve water utilization rates and strengthen water conservation management. In the area around our Val de Loire factory in France, rainfall volumes are expected to fall in future. Therefore, we regularly share information with other local industries on good water practices to decrease water consumption.
In cooperation with our stakeholders, we conduct water footprint assessments to better understand the environmental impact of water usage throughout our value chain. We ask our suppliers to provide information on their water usage through self-assessment and strive to ascertain water-related environmental impacts. In addition, we have participated in the "Study Group on Water, Climate Change and Sustainable Development" organized by Professor Oki Taikan of the University of Tokyo, who has outstanding expertise in hydrology, to gather the latest scientific knowledge on the characteristics of water resource, water availability, and the future change forecast associated with climate change. We apply these findings to our analysis of risks and opportunities related to climate change to ensure sustainable water use.
Reducing Waste
As population growth continues and income levels rise, resource consumption and waste increase. To make more effective use — and reuse — of limited resources, it is important that businesses shift from a disposable, linear economic model to a circular economy.
At Shiseido, we are doing this by optimizing the use of raw materials and reducing waste throughout our entire value chain, while complying with all relevant waste management rules in the countries and regions where we operate.
Reducing, Reusing and Recycling Waste
At Shiseido, we continuously work to reduce, reuse, and recycle the waste we generate. In 2003, we achieved “zero emissions“ at our domestic factories in Japan, and we continue our waste separation and recycling activities to this day. For example, to minimize the amount of sludge generated by our factories during wastewater treatment, we use dehydrators and dryers, recycle cardboard boxes and paper, and reuse shipping boxes. We also compress and melt waste plastics to both reduce waste volume and convert waste into valuable resources.
Our target was to achieve zero waste to landfill from our factories worldwide by 2022. Thanks to the actions above and other initiatives, we managed to achieve our target in 2020, two years ahead of schedule, and continue to achieve it.
To constantly improve our efforts to reduce, reuse and recycle, we are engaging in various initiatives to minimize waste generated outside of our factories and branch offices. This includes streamlining our product containers and packaging, eliminating package inserts, and shifting to more lightweight cardboard boxes. Moreover, we also work to limit product waste by minimizing excess inventory through improved precision in demand forecasts and shorter lead times in production and procurement.
Employee Education
All our waste reduction initiatives are driven by our PEOPLE. Therefore, we arrange online seminars and training sessions for newly appointed managers and employees in charge of industrial waste in Japan. Following the seminars and training sessions, each participant should be able to identify how to effectively manage waste with the help of our internal guidelines and checklists.